ステンレス製シンク(流し)の製作過程
既製品のシンクは金型で大量生産を目的としたもので、寸法も100ミリごとなどの寸法にしか対応しておらず1ミリ単位での製作に対応しておりません。
また、金型によるプレス加工では長尺ものは加工が難しく、ねじれやひずみなどがでてしまうため作るのは難しいようです。
しかし、当社ではシンクを展開した(折り紙のように立体をひらいた状態のこと)1枚のステンレスの板を立体に曲げ溶接して仕上げるため色々な寸法、形状に対応が可能です。
ここでは、当社の製作過程をご案内致します。
1.タレットパンチプレスで形状作成
3次元CADで立体をつくり、展開をします。
どういう金型で切り抜くかCAMと呼ばれるソフトで金型を配置し、それをCAMがNCコードと呼ばれる数値座標制御に変換し、それをタレパンのプログラムに読み込ませて任意の形状にします。
2.曲げ加工
タレパンで抜けた板をプレスブレーキで曲げ、立体型を完成させます。ここまでくればなんとなくシンクだとわかるような形状になります。
3.溶接
2で曲げた板の天板と言われる箇所を突き合わせ、TIG溶接をしていきます。
ステンレスは溶接する際にひずみが出やすく溶接するのが難しい材料です。
ステンレスや鋼板のひずみの原因として熱による膨張があります。TIG溶接は他の溶接方法に比べ小電流で火花が小さく、溶接個所に集中してアークを出せるためひずみを抑えることができます。
天板を付けたのち、シンク内部の四隅を専用の金型を使用し、少しずつハンマーでたたきながらR形状に曲げていきます。
その曲げた箇所を突きつけ、さらに溶接をしていきます。溶接をしてハンマーではたいて形状を整える、この作業を繰り返し行いシンクの底から立ち上がった四隅の部分を形成していきます。
4.仕上げ
溶接が全て終わると、天板の溶接箇所をグラインダーと呼ばれる機械で研磨していきます。
表面を荒削りし平らにしていきます。そしてフレキという研磨布で研磨したのち、ハイラップというさらにきめ細かい研磨材で研磨しピカピカに仕上げていきます。
つぎにフラップホイルという研磨材を使用し四隅の仕上げをしていきます。はじめは荒目の#80で研磨をし、凸凹が平になったら#240でさらに研磨をします。最後は#320で磨き上あげていきます。
最終的な仕上げはHL、#400といったステンレスの種類にもより違います。
下の画像は#400を使用して製作しています。
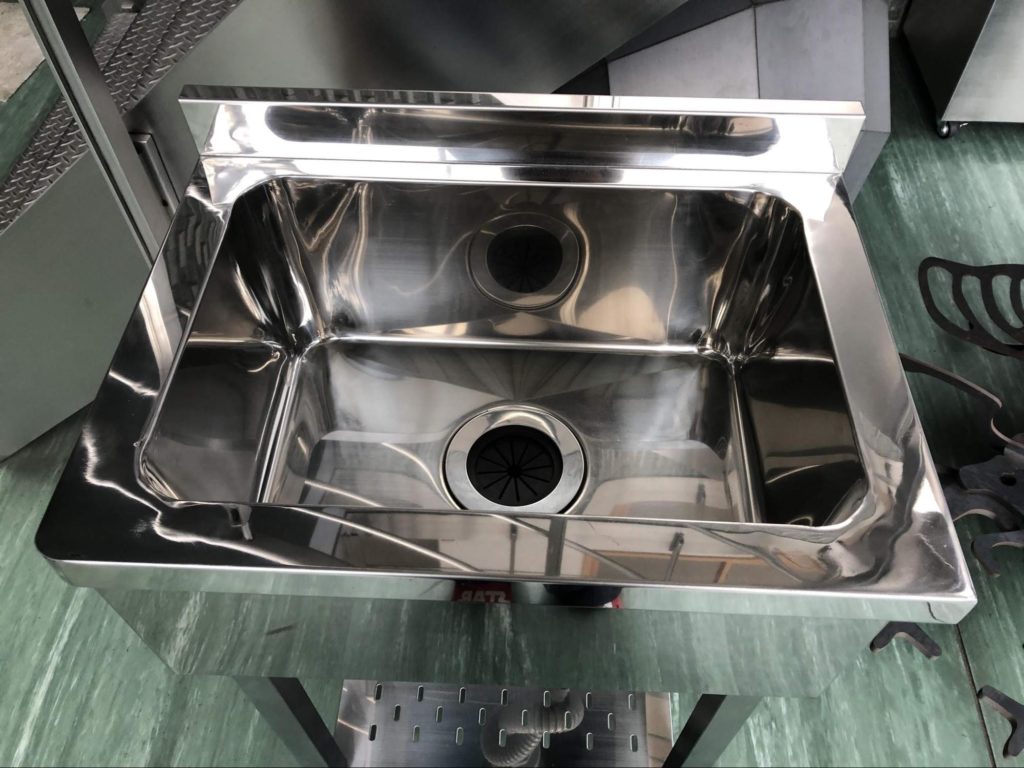
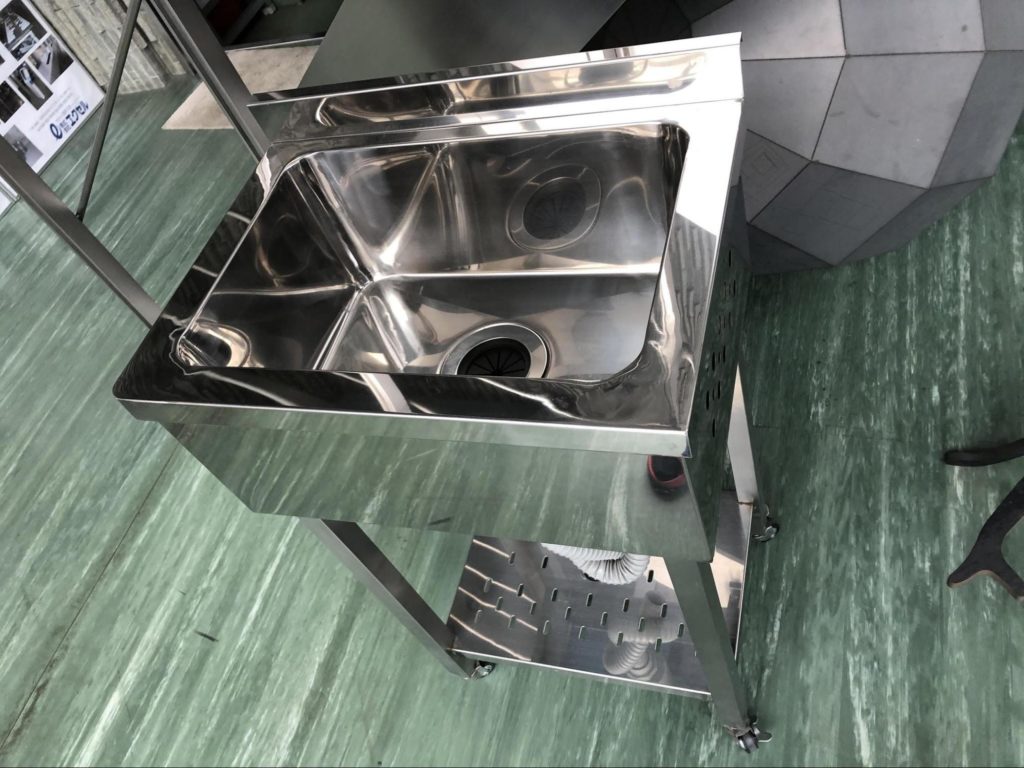